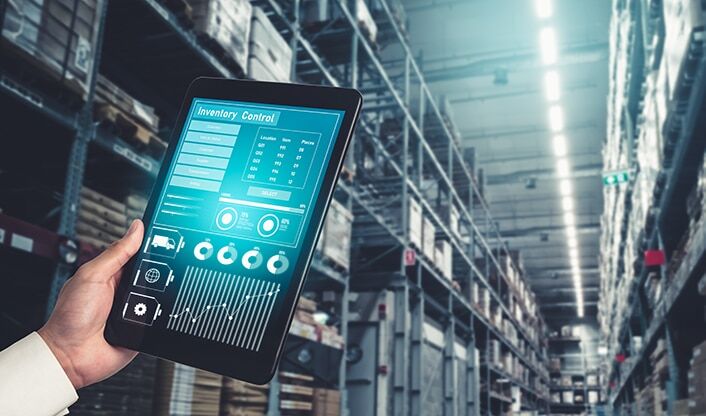
Table of Contents
Demand Planning:
The first step in effective inventory planning is understanding your customer demand. You will need to develop a demand forecast that considers both historical sales data and expected future trends. This will give you a good idea of how much inventory you will need to have on hand to meet customer demand.
Supply Planning:
Once you have a good understanding of customer demand, you can begin to plan your supply. You will need to determine how much inventory you can realistically produce or procure given your production capacity and lead time. It is important to build in some flexibility into your supply plan so that you can adapt to changes in demand. For example, if you suddenly receive an influx of orders, you may need to source additional inventory from suppliers or increase overtime production shifts. Conversely, if demand falls short of expectations, you can reduce production or cancel orders with suppliers.
Safety Stock:
No matter how well you plan, there will always be some degree of uncertainty when it comes to forecasting customer demand. That’s why it’s important to maintain a safety stock of inventory. This safety stock acts as a buffer in case demand is higher than expected or there are delays in procurement. The size of your safety stock will depend on the degree of uncertainty in your forecast and the frequency with which you replenish inventory. Maintaining too large of a safety stock can tie up capital and lead to storage costs, so it is important to strike a balance.
Inventory planning is essential for ensuring that your company has enough inventory on hand to meet customer demands. By understanding customer demand and forecasting future trends, you can develop a plan for procuring or producing the necessary amount of inventory. However, it is also important to maintain a safety stock in case of unexpected changes in demand or delays in procurement.